Why Powder Metallurgy is Ideal for Complex Metal Parts
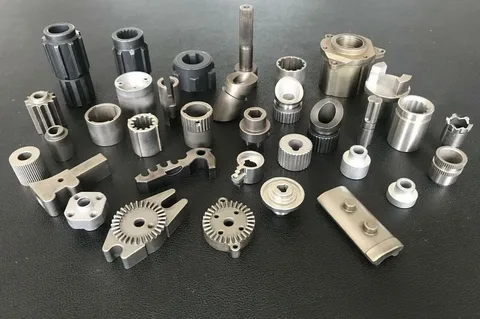
Powder metallurgy (PM) is a unique manufacturing process that has gained widespread popularity for producing complex metal parts. This process involves the production of metal powders, which are then compacted and heated to form solid components. Unlike traditional methods, such as casting or forging, powder metallurgy allows manufacturers to create intricate designs that would be difficult or expensive to achieve through conventional machining processes. The ability to precisely control the material composition and part geometry has made powder metallurgy ideal for industries that require high-performance parts, such as automotive, aerospace, and electronics.
The demand for complex metal parts is ever-increasing due to the advancements in technology and the need for more efficient, lightweight, and durable components. Traditional manufacturing methods often struggle to meet the requirements of producing parts with precise shapes, sizes, and material properties. This is where powder metallurgy excels, offering a viable alternative that combines efficiency with cost-effectiveness. In this article, we will explore why powder metallurgy is the ideal choice for manufacturing complex metal parts, highlighting its advantages, applications, and how it transforms the way parts are made.
Precision and Design Flexibility
One of the primary reasons why powder metallurgy is ideal for complex metal parts is its ability to achieve high precision and design flexibility. Traditional manufacturing processes often require multiple steps, such as casting, machining, and assembling, which can lead to a loss of material and intricate design features. In contrast, powder metallurgy allows manufacturers to create parts with near-net shapes, meaning that the final part is very close to the desired design without the need for extensive post-processing.
With powder metallurgy, intricate geometries can be produced with exceptional accuracy, which is particularly beneficial for industries where tight tolerances are required. For instance, in the automotive and aerospace industries, the production of gears, bearings, and other mechanical components requires high levels of precision to ensure proper function and safety. The ability to create parts with complex shapes, such as thin walls, small cavities, and interlocking features, is one of the key advantages of powder metallurgy.
Cost-Effectiveness for Mass Production
Another major benefit of powder metallurgy for complex metal parts is its cost-effectiveness, especially for mass production. Traditional manufacturing processes often involve significant material waste and long production times. Machining, for example, requires large amounts of raw material, which is then cut, milled, or turned to shape. This leads to material waste, which is both expensive and environmentally unfriendly.
Powder metallurgy, on the other hand, minimizes material waste by using powdered metal that can be compacted into the desired shape with minimal excess material. The process also eliminates the need for several additional steps, such as machining or forging, which reduces labor costs and energy consumption. Furthermore, the high-speed nature of powder metallurgy processes makes it suitable for large-scale production, where the cost per part decreases as the quantity increases. For companies looking to produce complex metal parts in high volumes, powder metallurgy offers a more efficient and affordable solution compared to traditional manufacturing techniques.
Material Versatility and Tailored Properties
Powder metallurgy offers an unparalleled level of material versatility, making it ideal for complex metal parts that require specific material properties. The ability to select and blend different metal powders allows manufacturers to tailor the properties of the final product to meet the specific needs of the application. For example, the strength, hardness, and wear resistance of the part can be optimized by choosing the appropriate combination of metals and alloying elements.
Additionally, powder metallurgy allows the incorporation of non-metallic materials, such as lubricants and ceramics, which can enhance the functionality of the part. This is especially beneficial in industries like automotive and aerospace, where components may need to withstand extreme temperatures, corrosive environments, or heavy loads. The precise control over the material composition during powder metallurgy processing ensures that parts are engineered to perform at their best, providing manufacturers with a high degree of control over the final product’s properties.
Minimal Waste and Environmental Impact
In today’s manufacturing landscape, there is increasing pressure to reduce waste and minimize environmental impact. Powder metallurgy stands out in this regard by generating less material waste compared to traditional manufacturing methods. In processes such as casting or machining, large amounts of material are often discarded as scrap, contributing to inefficiency and environmental harm.
With powder metallurgy, the metal powder that is not used in the final part can often be recycled and reused, making it a more sustainable option for producing complex metal parts. The compacting process generates little excess material, and the parts can be produced with minimal waste, reducing the overall environmental footprint of the manufacturing process. Additionally, since the process operates at lower temperatures than processes like casting or forging, it consumes less energy, further reducing its environmental impact. As industries increasingly focus on sustainability, powder metallurgy’s efficiency and reduced waste make it a compelling choice for producing complex parts in an eco-friendly manner.
Wide Range of Applications in Critical Industries
The versatility of powder metallurgy makes it suitable for a broad range of applications, particularly in industries where the complexity of parts is a crucial factor. In the automotive industry, for instance, PM is widely used to produce components such as piston rings, camshafts, and connecting rods. These parts require precise geometries and specific material properties to perform reliably under high-stress conditions. Powder metallurgy’s ability to produce parts with complex shapes and tailored material properties makes it the ideal choice for such demanding applications.
Similarly, in the aerospace industry, where components must withstand extreme temperatures, pressure, and mechanical stresses, powder metallurgy is employed to create high-performance parts like turbine blades, engine components, and heat exchangers. The ability to customize the material properties of these parts to meet the specific demands of the aerospace sector is one of the key reasons why powder metallurgy is so widely adopted in this field. Moreover, powder metallurgy is also used in the production of medical devices, electronics, and industrial machinery, demonstrating its adaptability across various industries that require complex, high-precision components.
Conclusion
Powder metallurgy has proven itself to be an ideal method for manufacturing complex metal parts, thanks to its precision, cost-effectiveness, material versatility, and environmental benefits. The ability to create parts with intricate geometries and tailored material properties makes powder metallurgy an invaluable tool for industries like automotive, aerospace, and electronics. By offering a more efficient and sustainable solution compared to traditional manufacturing techniques, powder metallurgy is transforming the way complex metal parts are made.
As industries continue to demand higher performance, lower costs, and greater customization, powder metallurgy will play an increasingly important role in meeting these challenges. Its ability to produce parts with minimal waste and energy consumption aligns with the growing focus on sustainability in manufacturing. Whether for small-scale production or large-volume manufacturing, powder metallurgy offers a flexible and reliable approach to producing complex, high-quality metal parts. The continued evolution of powder metallurgy technologies will likely further expand its capabilities, making it an even more attractive option for a wide range of industries in the future.